+886953128510

News
Konfu’s zinc plating process
2022-04-28
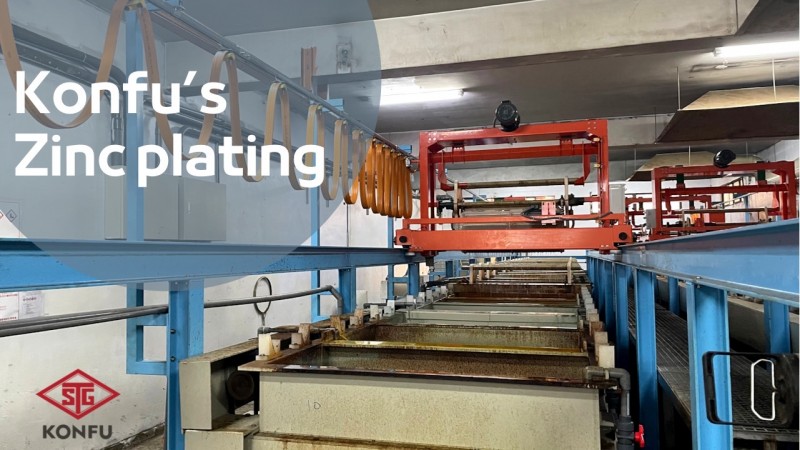
This month we’d like to introduce our plating process. The reason for plating is primarily for corrosion resistance and to increase product life. The main plating process includes loading, degreasing, pickling, zinc plating, phosphatizing, dehydrating, drying, unloading, and inspection. Water rinsing will be followed by every process to ensure better application.
The widely used way to plate screws is called barrel plating where all to-be-plated parts are poured evenly in a barrel and rotated. The parts are firstly cleaned of substrate such as cutting oil from the surface prior to plating. It’s an essential step because any dirt or contaminants remaining on the surface will prevent proper adhesion of the zinc plating. An alkaline detergent solution is used for surface cleaning. We extend the degreasing tanks from the common 4 tanks to 8 tanks, to extend the length of immersion and clean the surface completely. The degreasing process is followed by the application of an acid treatment (hydrochloric acid) to remove surface rust, which is called pickling.
Zinc plating, also known as electro-galvanising is a process where zinc is applied by using a current of electricity. Screws are plated with zinc for better corrosion resistance. Zinc plating applies a thin plating ranged from 0.2 - 0.5 mil of zinc to screws, giving them a layer of protection from the surrounding environment. The principle is that zinc reacts with oxygen and acidic compounds more strongly than steel and iron do and will be corroded before steel and iron are. We extend the plating tanks from often seen 12 tanks to 14 tanks to prolong the immersion for a better performance of plating.
Passivating is the process before dehydrating that involves the use of chromate based solutions to create a protective outer layer over the plated pieces. We choose trivalent chromium passivation and give up commonly used hexavalent chromium passivation to meet our customer’s specifications and reduce hazardous waste. After all the above processes, the screws are sent to the drying machine and packed after thorough inspection.
